That's a Wrap!
Two GOEBEL IMS slitter rewinders were completely overhauled after more than 30 years of service. The cabling, which is exposed to high stresses, required a special solution.
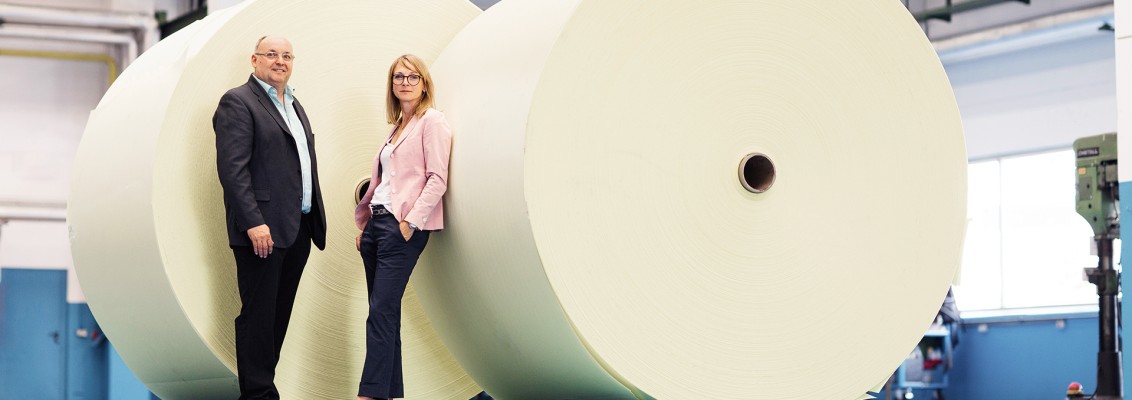
It’s often the small, insignificant things in life that are difficult to make. Who asks themselves while making a cup of tea how the very delicate filter paper became a tea bag? And which smoker stops to think how the thin cigarette paper got its shape? These and all other types of paper, cardboard, film and foil have one thing in common: their processing began on a giant roll. Step by step they are reduced to their final size by slitter rewinders. Since paper, cardboard, film and foil all have unique properties, GOEBEL Schneid- und Wickelsysteme GmbH has the right machine for each of them. The company, located in Darmstadt and other sites, can look back on more than 165 years of history. Group Marketing Manager Kerstin Stumpf-Trautmann explains: “Our plants cover five market segments: aluminium and plastic films, aseptic packaging materials, papers, cardboards, and cigarette papers. The expectations placed on our slitter rewinders in terms of quality, workmanship and precision are particularly high in all of these markets. We’ve been meeting them for decades, and our technical solutions for slitting and rewinding have developed us into a renowned supplier and market leader in standard and specialised machines.“
LIKE NEW AFTER 30 YEARS
GOEBEL IMS also focuses on the maintenance and modernisation of more than 11,000 slitter rewinders shipped around the world. When two MONOSLIT slitter rewinders had to be retrofitted after 30 years in use, experts carefully analysed the complete system. Harald Loos, head of electrical design at GOEBEL IMS explains: “The machines are used to cut plastic film for packaging. One machine was in a production plant in Canada, the other in the USA. Both needed to be modernised to meet future requirements, including the cabling. Cables and wires in particular have seen many changes in the past decades and we wanted to integrate the new developments into the retrofit.” The Darmstadt company therefore turned to the experts at HELUKABEL for the redesign of the custom cable.
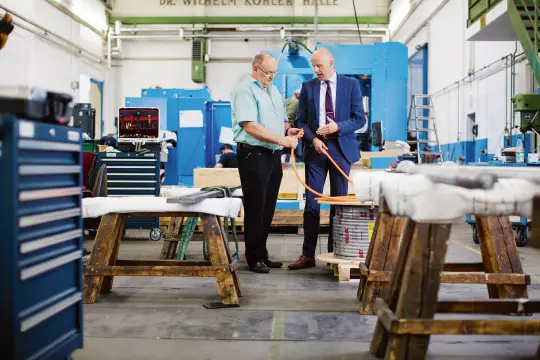
HIGH DEMANDS
When cutting paper, film, or foil, the web of material is first unwound from an original roll up to 12 metres (39 feet) wide onto the slitter rewinder and cut lengthwise into narrower strips. These webs are then fed into so-called winding stations where they are rewound in the new width. A winding station comprises two winding arms, up to 48 of which can be mounted on the traverses of the slitter rewinder. The winding arms move in two dimensions: to the left and right to adjust to the desired width of the web, and forward in a swivelling motion. Sensors and actuators such as command devices, AC servomotors, positioning drives, and valves are installed in each winding arm to implement the rewinding and movement processes. The custom cable implemented here must not only contain the power, feedback and servo cables for driving the motor, but also a number of data cables. During machine operation, the cable is carried along in an uncontrolled manner, exposing it to very high mechanical forces. Claus Müller-Bohrmann, regional sales manager at HELUKABEL, reports: “The development of the custom cable posed several challenges. One thing we wanted to do was add more data wires without greatly increasing the diameter of the existing cable. Even more important however, was balancing the tensile and compressive forces.”
Anton Giss, cable designer at HELUKABEL in Windsbach, Bavaria, set to work on implementing these specifications: “On the basis of the terminal diagram and the actual power consumption, we discovered that the previously used power cable was oversized. Instead of the previous four square millimetre (12 AWG) cross-section, we are able to provide an adequate power supply with a cross section of just two and a half square millimetres (14 AWG). This provided space for the additional wires and allowed a thicker sheath to be put around the custom cable, which in turn improved service life and allowed for more abrasion resistance when 'dragging’ the cable.”
"With the new cabling, the machines are equipped for the next 30 years."
-Harald Loos, head of electical design at GOEBEL IMS
THE BREAK-PREVENTION TRICK
The Windsbach experts also used simulation techniques to calculate the optimal screening to guarantee interference-free wires in the sheathing; a special foil layer stops the individual wires from rubbing against each other. The two-dimensional movement of the winding arms creates tensile force in the cables. Giss: “To absorb this force, we inserted a so-called strain-relief braid between the inner and outer sheaths.” Harald Loos adds: “We also designed a custom fixing clip to attach the cable to the winding arms. The clip is only fixed to the outer sheath of the cable. The internal braid restricts the mechanical tension on the sheath.” To stop the cable cores from breaking, the HELUKABEL experts inserted special high-tensile and compression-resistant filler into the cable during the stranding phase of production. Giss: “This maintains the mobility of the cable while preventing too tight a bending radius.” In the meantime, the two refurbished MONOSLIT slitter rewinders are back in operation and Harald Loos is optimistic— “With the new cabling, the machines are equipped for the next 30 years.“
THE SLITTING AND WINDING EXPERTS
Who: The GOEBEL Schneid- und Wickelsysteme GmbH/Germany is part of the IMS TECHNOLOGIES S.p.A. mechanical engineering group and employs more than 100 people at its Darmstadt site.
What: Under the GOEBEL IMS brand, the company develops, among other things, slitter rewinders, automatic reelers, and winders. The cutting machines are used to process paper, cardboard, packaging and industrial films, as well as aluminium foil, aseptic packaging and other special materials.